Mycobot Toolkit: Exploring The Robotic End-effectors
About the project
Discover the power of robotic arm end-effectors! Dive into their unique features, understand their applications, and find the right fit!
Project info
Difficulty: Easy
Platforms: Elephant Robotics
Estimated time: 1 hour
License: GNU General Public License, version 3 or later (GPL3+)
Items used in this project
Software apps and online services
Story
Hello,today's article focuses on explaining and showcasing the various accessories available for the myCobot 280. We aim to provide a clear understanding of the functions these end effectors can perform, assisting you in selecting the most suitable accessory for your needs. Specifically, this article will introduce four commonly used end effectors for this robotic arm.
ProdcutmyCobot 280 M5StackThe myCobot 280 is the world's smallest and lightest 6-DOF collaborative robot. Despite its compact size, the myCobot 280 boasts impressive power and features a wide range of hardware and software interaction methods, as well as diverse compatible expansion interfaces. It offers extensive support for secondary development across multiple platforms, effectively enabling users to create applications in various scenarios.It is mainly suitable for disciplines related to artificial intelligence, personal creative development, exploration of commercial applications, and other scenarios.
The myCobot 280 driver library facilitates secondary development and is compatible with puzzle programming, code programming, manual drag-and-drop applications, robot simulation programming, and other development control methods. This versatility provides users with a plethora of options for controlling the robot and tailoring it to their specific needs.
Robotic arm: myCobot 280 M5stack
Programming language: Python, myBlockly
Operating system: Windows 10/11
myCobot adaptive gripperThe myCobot adaptive gripper is suitable for a variety of consumer-grade models. It uses serial communication control, can automatically adapt to the width of the object being gripped, and can control the size of the gripper opening and closing, providing multiple programming language control interfaces.
Programming control with python
from pymycobot.mycobot import Mycobot
mc = Mycobot('com3',115200)
#Zero calibration of gripper
mc.set_gripper_calibration()
# Opening and closing of gripper
0 is close,1 is open;int speed : 1~100
mc.set_gripper_state(0/1,speed)
# Control of the clamping distance of the gripper
int degree:0~100;int speed : 1~100
mc.set_gripper_value(degree,speed)
Example:
mc.set_gripper_value(100,80)
time.sleep(1)
mc.set_gripper_value(50,80)
It is mainly suitable for the following scenarios:
● The width of the object to be gripped is between 25~45mm
● The weight should not exceed 150g (the maximum end load of the robotic arm is 250g)
● The material of the object should be hard enough to avoid deformation.
myCobot Suction pump 2.0The myCobot suction pump operates based on the vacuum adsorption principle, utilizing atmospheric pressure to securely hold objects. When the suction cup is attached to the surface of an object, the air within the cup is extracted, creating a pressure differential that enables a firm grip. The greater the pressure difference, the stronger the adsorption force. It provides standard 3.3V IO control and can be widely used in various embedded device developments.
Programming control with python
from pymycobot.mycobot import Mycobot
mc = Mycobot('com3',115200)
#control Suction pump
IO port is the location where the suction pump is connected to the IO interface of the robot arm
state : 0 is open; 1 is close
mc.set_basic_output(IO port,state)
Example
#open the suction pump
mc.set_basic_output(5,0)
time.sleep(5)
# close the suction pump
mc.set_basic_output(5,1)
It is mainly suitable for the following types of objects:
● Objects with a smooth and flat surface: The suction pump relies on the principle of atmospheric pressure difference, which may not work effectively on rough or uneven surfaces.
● Objects of moderate size: It is not recommended to use the suction pump for picking up large-volume objects, as they may not remain stable during the movement of the robotic arm.
● Objects weighing up to 150g: The suction pump is designed to handle objects within a weight limit of 150g. Exceeding this weight limit may compromise the stability and effectiveness of the suction grip.
Now, let's move on to introducing another special suction pump.
Double head suction pumpThe double head suction pump has two suction heads, made of CNC metal parts and photosensitive resin. It can adsorb larger volume objects. The working principle of the double head suction pump is the same as that of the suction pump 2.0, which is to create an atmospheric pressure difference. It provides standard 3.3V IO control and can be widely used in various embedded device developments.
The control method of double head suction pump is the same as that of suction pump 2.0.
Programming control with python
from pymycobot.mycobot import Mycobot
mc = Mycobot('com3',115200)
#control Suction pump
IO port is the location where the suction pump is connected to the IO interface of the robot arm
state : 0 is open; 1 is close
mc.set_basic_output(IO port,state)
Example
#open the suction pump
mc.set_basic_output(5,0)
time.sleep(5)
# close the suction pump
mc.set_basic_output(5,1)
It is mainly suitable for the following types of objects:
● Objects with a smooth and flat surface: The suction pump relies on the principle of atmospheric pressure difference, which may not work effectively on rough or uneven surfaces.
● Objects weighing up to 150g: It is recommended to adhere to the maximum load capacity of 250g at the end of the robotic arm. Thus, objects exceeding 150g may compromise stability and performance.
● Objects with a larger surface area: The design of the dual-head suction pump is specifically tailored for picking up larger objects, making it well-suited for applications that require gripping objects with a substantial surface area.
● Increased stability with more suction heads: The double head suction pump benefits from multiple suction heads, which create a greater pressure difference and enhance stability during the gripping process.
Dexterous handThe Dexterous hand is an innovative end-effector designed to replicate the functionality of the human palm, enabling bionic imitation for tasks such as object grasping and placement. It operates primarily through IO control and power control methods, allowing for precise and coordinated movements.It's important to note that the Dexterous hand is currently in the development phase, and this article serves as an initial introduction to it.
1 / 2
It is mainly suitable for the following scenarios:
● The Dexterous hand is mainly used for grasping and placing irregular objects.
● The weight of the object to be grasped needs to be controlled within 100g.
● The width of the object should be controlled between 25mm-45mm.
SummaryIn this article, I have introduced four excellent end-effectors for robotic arms. By exploring the functionalities and characteristics of each effector, we can see their unique advantages in different application fields. When choosing an end-effector for a robotic arm, you need to consider which one can meet the needs of your scenario, whether it's for simple movement tasks or for performing some cool actions.
If there are any other end-effectors you want to learn about, feel free to leave a comment below the article. Your comments and likes are the greatest support for us! See you next time.
Credits
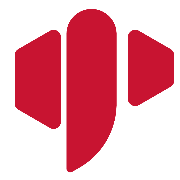
Elephant Robotics
Elephant Robotics is a technology firm specializing in the design and production of robotics, development and applications of operating system and intelligent manufacturing services in industry, commerce, education, scientific research, home and etc.
Leave your feedback...