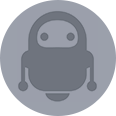
Great Helper For Robotic Arms, Pneumatic End Effectors
About the project
Introduction to the parameters and use of three types of pneumatic end-effectors.
Project info
Difficulty: Easy
Platforms: Elephant Robotics
Estimated time: 1 hour
License: GNU General Public License, version 3 or later (GPL3+)
Items used in this project
Software apps and online services
Story
Topics
Here we would like to introduce how the pneumatically driven end-effectors can be used in connection with the myCobot 320. What can they do respectively?
We have already written an article on the myCobot320 electric gripper, for more information, you can check it out: Electric gripper
A summary of the article on electric grippers:
● What is a gripper?
● How the grippers are driven?
● Parameters and scenarios for two electric grippers
Pneumatic VS ElectricIn the current field of industrial automation, pneumatically driven end-effectors still dominate the market because of the low cost of equipment, the abundance of product models and the wide range of applications.
Electric end-effectors use electricity instead of high pressure air as energy.Compared to hydraulic end-effectors, the system is easy to maintain and does not require the use of hydraulic energy, which reduces energy pollution.
Electric end-effectors are superior to hydraulic and pneumatic end-effectors in terms of performance and structure and are the future trend in the end-effector industry. For the time being, pneumatically driven end-effectors still occupy a leading position in the industry.
myCobot 320We still use the myCobot 320 for adaptation to pneumatic driven devices.
myCobot 320 is a six-axis robotic arm with a wide range of functions that can be equipped with various actuators, such as grippers, suction pumps, etc. It is particularly suitable for education and research.
myCobot 320 has a wealth of open source resources and support many development methodes such as python, c++, c#, etc.This allows the users to set up and get the application run quickly, even beginners can easily operate the robotic arm.
Here are the pneumatic devices we will talk about. Three in total, two grippers and a suction pump.
EquipmentsAir CompressorWhat is the source of energy for pneumatics? It is the high air pressure. We need a machine to create high air pressure to provide the energy source for the pneumatic equipment. The picture below is a air compressor.
Once the air compressor is energized, it can accumulate high-pressure air in the machine to provide power for subsequent use.
Soft gripper Function: To grab objects (larger size)Introduction:● When we use other grippers to grab, it is easy to damage the surface of objects, the soft-touch gripper grips the panel or component with a pinched edge, ensuring a flawless surface and improved yield.
● The modular design of the soft-touch gripper is lightweight and can be freely arranged and combined according to panel size.
● The clamping force of conventional cylinders is generally large and difficult to control, and the edges of the clamping panel can be easily pinched and warped.The single finger gripping force of the soft gripper is precisely controlled and will not pinch fragile workpieces.
Working principle:The soft gripper is an innovative bionic flexible tool developed by researchers to mimic the morphology of a starfish's wrist. The "fingers" of the soft claw are made of a flexible polymer silicone material, which is inflated for bending deformation and can be adaptively wrapped around the target object, like a starfish, to complete the perfect grab on shaped and fragile objects.
The chart below shows its parameters.
● The pneumatic gripper, also known as the pneumatic finger or pneumatic finger, is an actuating device that uses compressed air as a power source to grip or grasp workpieces. It is small in size, light in weight, compact in shape, can achieve single and two-way gripping, can be automatically aligned, has high repeatability and the magnetic switch allows for automated control.
● Its main function is to replace human gripping work, which can effectively improve productivity and work safety.
Working principle:● Single piston: In contrast, the shaft drives the crank and the jaws are driven by the piston to open and close the movement. Each of the two jaws has a corresponding crank slot. To reduce frictional resistance, the jaws are connected to the body by a steel ball slide.
● Double pistons: It is actuated by two pistons, each piston is connected to the pneumatic fingers by a roller and a double crank, forming a special drive unit. The pneumatic fingers are always axially aligned and each finger cannot be moved individually. If the fingers move in the opposite direction, the previously pressurised piston is exhausted and the other piston is pressurised.
The chart below shows its parameters.
Function: To absorb larger and heavier objects
Introduction:● Vacuum suction pump is a suction port that draws a vacuum to the suction cups, causing the internal air pressure to change from atmospheric pressure to negative pressure, using the pressure difference between the external atmospheric pressure and this negative pressure to achieve the purpose of adsorbing the object.
● The overall construction is multifunctional and extendable suction cups for up to 4.
Working principle:● The vacuum device is activated to create a negative air pressure in the suction cups, so that the object to be lifted can be transported by sucking it into place.
● When the object is transported to its destination, it is smoothly inflated into the vacuum suction cup, so that the vacuum suction cup becomes zero or positive air pressure from negative air pressure, and the vacuum suction cup is detached from the object.
The chart below shows its parameters.
Video
Here is the video shows how to install and operate the equipment.
SummaryHave you found an end-effector for your robotic arm after two articles? Electrically driven or pneumatically driven? They each have their advantages, and the choice of end-effector depends on the environment in which it is used. If you have any questions you'd like to ask, feel free to leave a comment below! Your likes and comments are our motivation.
Credits
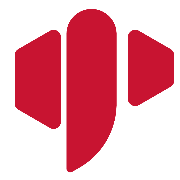
Elephant Robotics
Elephant Robotics is a technology firm specializing in the design and production of robotics, development and applications of operating system and intelligent manufacturing services in industry, commerce, education, scientific research, home and etc.